A tractor must not only be powerful, but also look good – especially when it rolls off the production line. After all, the John Deere green is an integral part of the brand. By implementing the new fully automatic painting system, the company is continuing to modernise its tractor production at the Mannheim site and set new standards in terms of paint quality, environmental protection and energy efficiency.
The investment of 80m € – will then need to be converted to pounds) in the new paint shop and modernisation of the final assembly line is also an important commitment to the largest John Deere site outside of North America.

Hi-tech for perfect surfaces
On the new line, the tractor chassis first pass through seven cleaning and preparation stages, involving four robots. Following that, 10 robots work in perfect harmony to apply the primer, followed by the green final coat. A control centre is responsible for monitoring and operating the plant.
Did you know?
How many tractor chassis can be in the paint shop at the same time?
- About 50 chassis
- About 100 chassis
- About 150 chassis
Solution:
The paint shop has the capacity to process around 100 chassis simultaneously, with each one being worked on at 2.7-minute intervals.
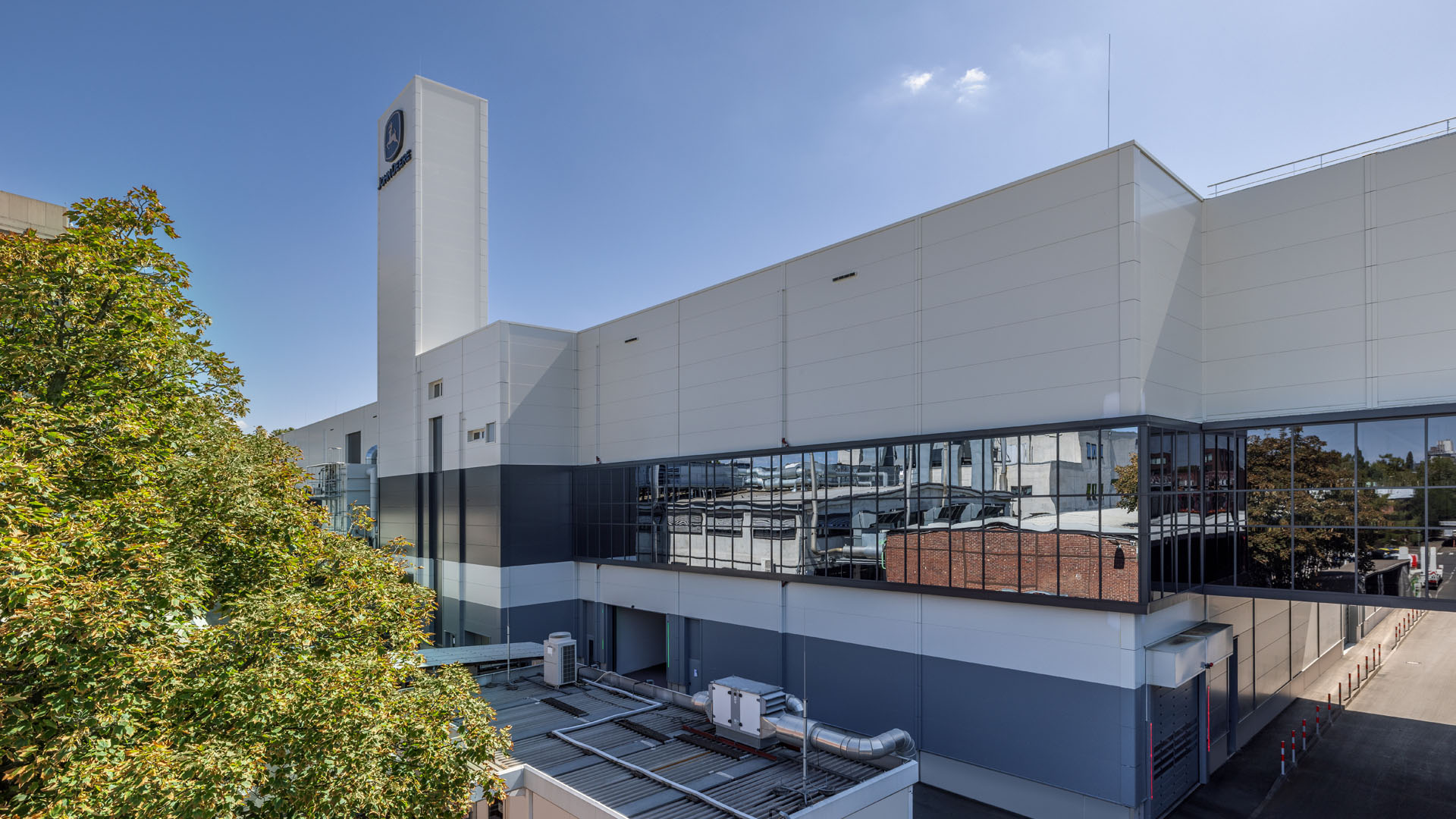
A green investment for the future
The new building is the first at John Deere to meet the KfW-40 efficiency level. Energy efficiency has been significantly improved thanks to optimal heat insulation and use of the latest technologies such as heat pumps and frequency converters. In addition, the exhaust gas post-combustion significantly reduces emissions, while wastewater and rubbish are largely avoided. In addition, the plant uses electricity generated by solar panels on the roof.
Did you know?
How much electricity can the solar panels on the roof of the new facility generate per year?
- 400.000 kWh
- 600.000 kWh
- 800.000 kWh
Solution:
The 3.600 m² of solar panels on the roof of the new building can generate up to 800,000kWh of electricity per year for internal use.
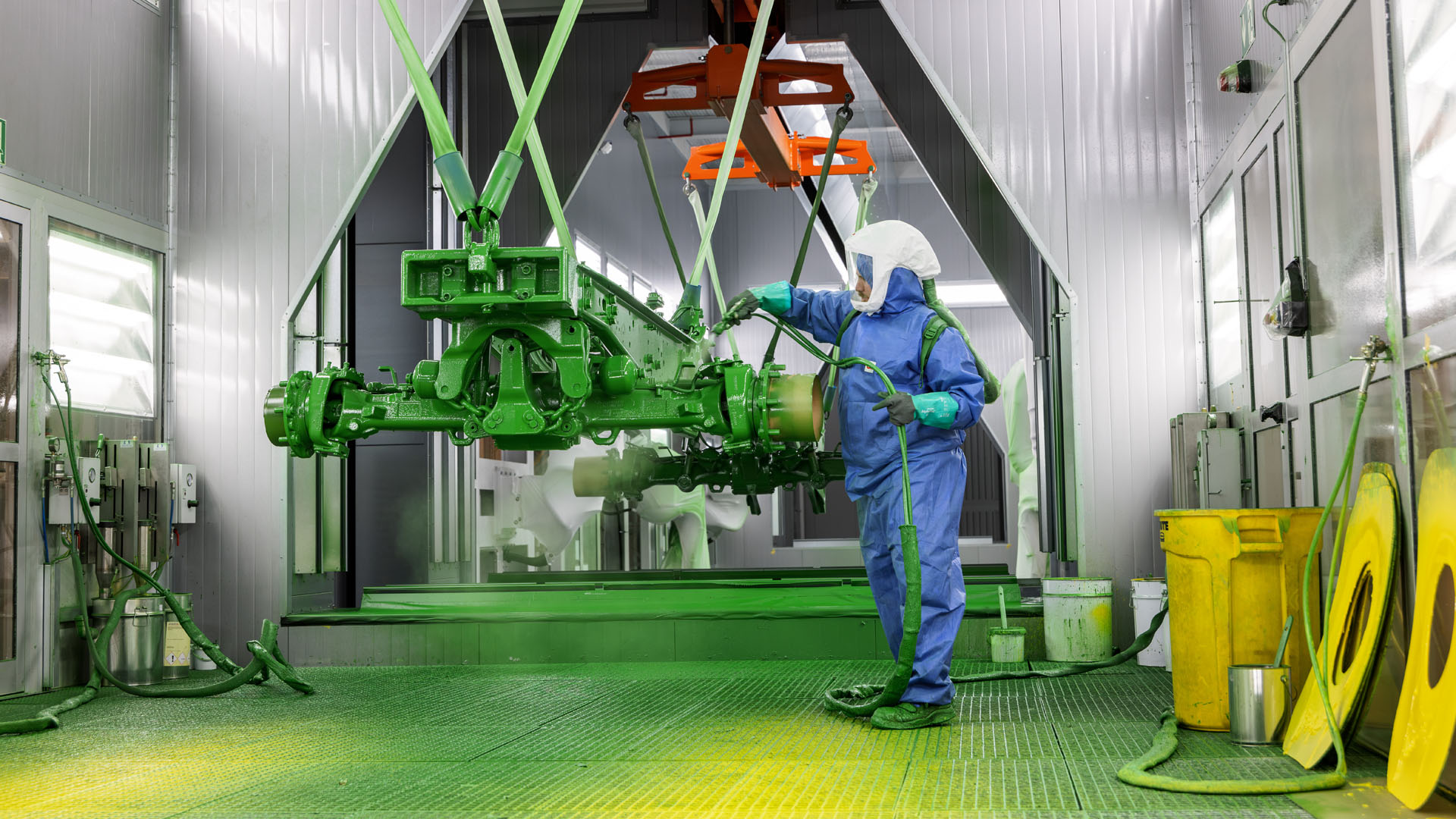
Quality, flexibility and human expertise
The paint shop not only strengthens production at the Mannheim site, but also enables the flexible production of larger tractors and various models. Despite full automation, human expertise remains indispensable as specialists operate the system, programme the robots and ensure quality in a special manual painting booth. At the end of the process, employees visually inspect the paintwork of each chassis before it enters the dryer.
Did you know?
What is the maximum weight of a tractor chassis that can be painted in the new plant?
- Up to 6.000 kg
- Up to 8.000 kg
- Up to 10.000 kg
Solution:
The new system is designed for tractor chassis with a tare weight of up to 8,000kg and a width of up to 3.5m.
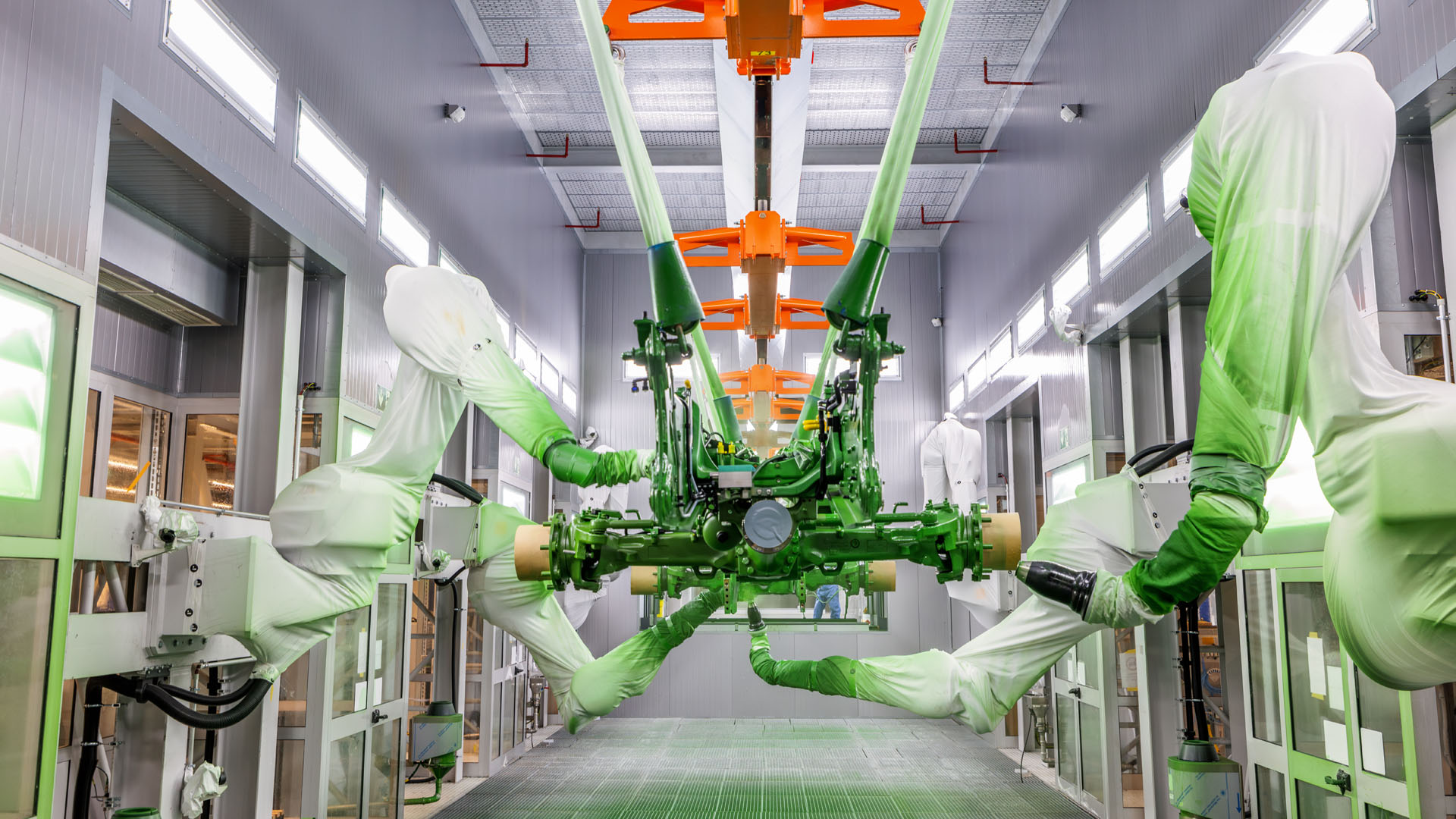
Innovation to help the environment
A highlight of the new system is the innovative way it handles overspray, i.e. paint that does not end up on the chassis. This makes a significant contribution to the environmentally friendliness and efficiency of the paint shop and replaces the wet scrubbing process used in the past, in which water was constantly running to catch the paint particles and which then had to be cleaned at great expense.
Did you know?
How is the overspray separated in the new system?
- By water walls
- By rotating brushes
- By an electrostatic precipitator
Solution:
In the new system, the overspray is separated by rotating brushes. The brushes trap the paint particles from the exhaust air, which are then regularly scraped off and disposed of without creating any additional wastewater. This method is environmentally friendly and conserves resources.

From the start of construction to production
The construction of such a complex plant is a massive undertaking that required careful planning and co-ordination. The project not only involved the building work, but also the installation, testing and optimisation of the complex painting technology. The final changeover from the old to the new plant took place within three weeks during the summer shutdown this year without affecting ongoing production.
Did you know?
How long did it take from the start of construction to the official opening of the new paint shop?
- About two years
- About three years
- About four years
Solution:
Almost exactly three years: Work began in November 2021 with the official opening taking place in October 2024.