France is unusual in that it produces as much winter barley as spring barley, both are intended for beer production, and totals nearly 4m tonnes annually. This is an asset on the global market because these diversified sources give brewers options for specific types of malt for different beers. Malt from six-row winter barley is suitable for producing abbey type beers and lagers. This malt is versatile and is often mixed with two-row spring barley malt, which is considered to be better quality by brewers but shows a higher variability in its brewing properties. From the producers’ point of view, the different types of malting barley are also interesting.

Six-row winter barleys provide the best yield, but while a little less productive, spring barleys are often valued higher due to their quality, grain size, specific weight, malt extract, germination speed and friability. As a result, the price paid for spring barley is often £13-17/t (€15-20/t) higher than winter barley.
Three types of barley on the same farm
Some farmers grow both winter and spring varieties. In Eure-et-Loir, Julien Doussineau has chosen a combined approach. “I have three sowing windows: Early autumn for winter barley, November for some spring barley and February or March for traditional spring barley,” he explains. “It makes sense to include these three crops in my rotation because they are harvested both before and after the wheat, which allows a smooth organisation of the harvest while spreading the risks.”

Three crops of malting barley in my crop rotation allow me to organise the harvest and spread the risk.
Julien Doussineau
This is because some crops prove riskier in terms of establishment. “On average, spring barley sown in winter is damaged by frost once every 10 years. In return, I get 1.5t/ha more yield than conventional spring sowing. I still grow spring barley traditionally – sowing in February, because it is a crop that is economical in inputs and allows us to break the cycle of resistant weeds, in particular ryegrass.”
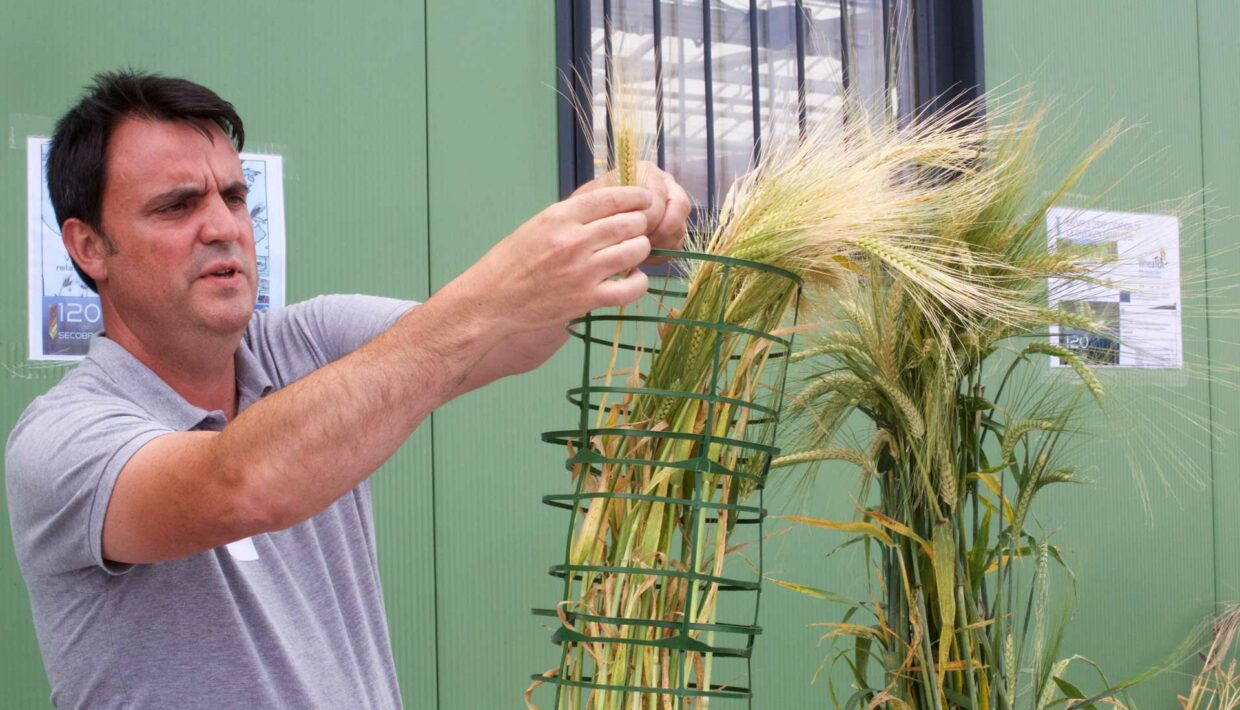
Julien farms nearly 600ha on a family farm in Boisville Saint Père (Eure-et-Loir) where he grows 10 different crops – his wells and irrigation system allow him to safeguard yields. “I have the right conditions to produce malting barley despite adverse weather. I am currently sowing four winter and spring malting varieties, and I also grow 35ha of four types of barley for seed.” The farm is well equipped for drying and storage, without which Julien wouldn’t be able to fulfil multiple contracts.
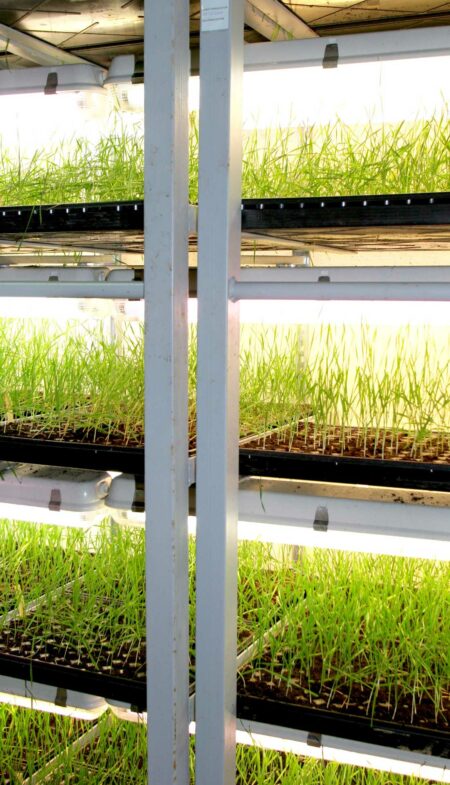
Further east in Burgundy, in a continental climate, winter malting barley occupies a good place in crop rotations. It allows for early autumn sowing, and harvest occurs before drought sets in. “Six-row winter barleys have an advantage in the context of climate change,” notes Mickael Mimeau of the co-operative Alliance BFC.
“It is one of the species most tolerant to the water shortages in the Burgundy-France region.” Winter barley yields are close to winter wheat yields, but with less variability. And compared to spring barley, the protein content is more stable. Even if the grain size of six-row winter varieties is lower, it is getting closer to that of spring barley, thanks to varietal progress.
It is for this reason that the Burgundy region today harvests an eighth of France’s winter barley. The latter has overtaken spring barley, which is less productive and more vulnerable to drought. “Winter barley offers agronomic advantages in the crop rotation in areas with low potential,” says Geoffroy Oudoire, an Arvalis (research institute) engineer.
“Moreover, barley has hulled grains, which partly protects them from pests and disease. Contamination is often lower than in other cereals.” In this central-eastern region, the profitability of barley remains closely linked to subsidies. “Prices paid to farmers have been increasing for two seasons, but we should keep a close eye on the margins this year, in the context of a sharp increase in inputs,” notes Geoffroy.
Effective selection for six-row barleys
Although six-row winter barley varieties are considered to be the all-purpose barley for malting and brewing, they are still improving. Selection is improving characteristics like grain size and malt extract. Research, particularly in genomics, has accelerated genetic progress, with varietal selection time halved in 20 years.
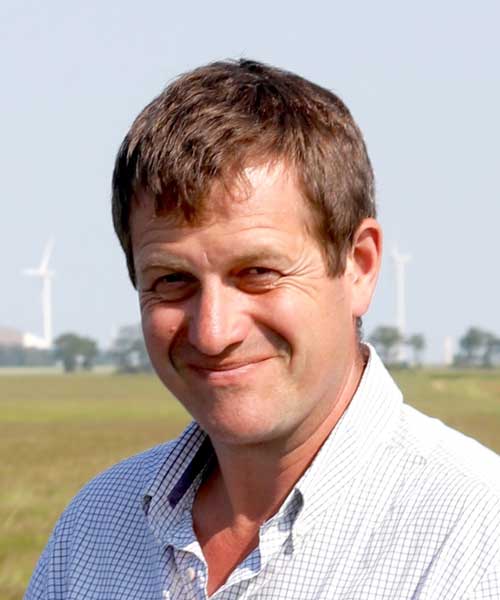
Our selection has drawn genes of interest from exotic population varieties.
Dominique Vequaud
On average, winter barley yields have increased by more than 0.1t/ha per year. Above all, disease resistance has gone up a notch. This was necessary following the ban on seed treatments using neonicotinoid insecticides, which protected barley from barley yellow dwarf virus (BYDV), transmitted by aphids. At a time when autumns are increasingly mild and favourable to aphids.
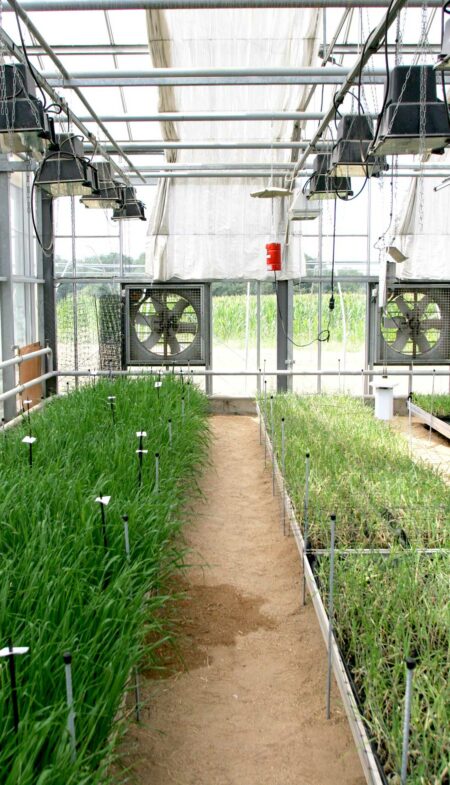
“Genetics remains the ideal solution”, says Florent Cornut, sales director at the seed company Secobra Recherches. “Our selection has drawn genes of interest to combat BYDV from exotic population varieties. Since 2019, 100% of the winter barleys that we submit for registration in France are BYDV-tolerant.”
As far as other pests are concerned, solutions are being deployed. “We have found a new source of resistance to rhynchosporium, a major barley disease, as well as sources of resistance to Wheat Dwarf Virus,” reports Dominique Vequaud, a barley breeder at Secobra Recherches. The other challenge for seed companies now involves offering local varieties to produce local beer in micro-breweries.
“And finally, we want to develop varieties requiring less nitrogen input, to reduce the carbon footprint of this crop,” adds Gilles Fouquin, director at Secobra Research. In the case of spring barley, one of the options would be to select varieties with a short 100-day growing cycle, with dwarf growth and low nitrogen requirements. “By changing the shape and growth rate of the plant, we are hopeful of being able to create barleys adapted to the new constraints.”
Reducing emissions
The entire barley and wheat malting sector is addressing other environmental challenges. And the first step is to improve proximity. “We want to encourage short supply chains for barley and hops. Given that 90% of French people today live less than 20 minutes from a brewery, we must develop the production of malting barley locally throughout France,” say industry representatives.
The other challenge for maltsters and brewers lies in reducing CO2 emissions and wastewater discharges. For several years, manufacturers have been committed to optimising resources, particularly energy and water. An environmental certification process has already made it possible to reduce water consumption by 20%.
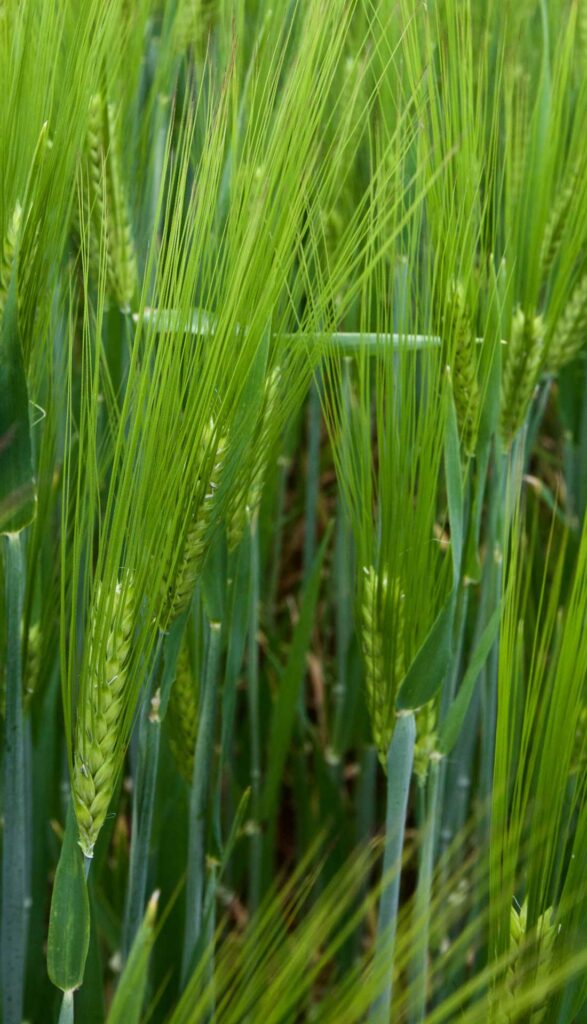

Maltsters have committed to going further, with a new objective of reducing water consumption by 25% by 2030. The target for brewers is by 40%, and already, new breweries have integrated water recycling into their systems. Ultimately, brewers are aiming higher, with the goal of achieving zero waste production by recovering all beer co-products like yeast and spent grains, while working on 100% recyclable packaging and cans.