This article was first published in “The Furrow” in April 2016.
The modern consumer is a demanding one. We want top quality food, produced to the highest welfare standards, at the lowest possible price. For today’s farmers, that presents a considerable challenge. But one pig producer in Dorset is striving to meet those demands, and has found a system that could be rolled out across the industry.
Robert Lasseter cut his farming teeth producing outdoor pigs in the rolling green hills made famous by Victorian novelist Thomas Hardy, author of Far From the Madding Crowd and Tess of the d’Urbevilles. “I bought a small herd of pigs and was selling 70kg porkers off a few rented fields,” he says.
But outdoor pigs did little to enhance this Dorset idyll, turning the green fields into muddy brown deserts populated by corrugated tin arks. “I could never answer the question: Why keep a woodland animal that likes damp shady conditions in an open field where the only shelter is a tin hut?”

Corton Farm is based in Thomas Hardy country, which looks prettier with its green fields than muddy outdoor pig ranges.
So in 2007, when Mr Lasseter moved the herd to Corton Farm at Friar Waddon, he became one of the UK’s few indoor pig producers approved under the RSPCA’s Freedom Food scheme. This paid him a 7p/kg premium for pork produced to high welfare standards – and since then he has continually developed and honed his system to maximise productivity, profitability and pig welfare.
A life changing investment
In 2014 Mr Lasseter made his biggest investment yet – and if it catches on it could transform the lives of millions of pigs each year. After intensive research and study tours, he decided to replace his farrowing crates with new farrowing pens that provide a far more natural environment for the sow and her piglets and meet the RSPCA’s upgraded standards.
“To me, it’s the difference between caged hens and those in a colony system,” he says. “I don’t like the idea of motherhood behind bars: The international pig industry is coming in for a lot of flack, and I think we need to change the way we farm.”
Farrowing crates were first introduced in the 1960s as a way to reduce piglet mortality. Although extremely effective, Mr Lasseter believes their days are numbered, as newer free farrowing systems offer a higher welfare alternative.

Free farrowing could be the system of the future, allowing sows to express natural behaviour while protecting the piglets.
Pioneering maternity unit
“I went to look at a number of different free farrowing systems, and learnt a lot from the pioneering farmers’ successes and mistakes,” he says. “Eventually we trialled 18 360° pens in an existing Finrone building, and after a few improvements invested in two batches of 26 pens.”
A major advantage of the 360° pens, from the farmer’s perspective, is that they fit on the same footprint as conventional crates. However, the floor may need to be replaced to ensure it’s strong enough to support the sow, as – unlike in crates – she has the space to turn around, move about and exhibit more natural behaviour.
The pens have sliding bars that offer protection to the piglets, as well as heat mats and an area for creep feed that Mr Lasseter designed himself. Open grids mean the sows and piglets can see their neighbours, while a lever-operated crush can isolate the sow for any management required.
The pens are bedded with shredded paper over the slatted floor, with ad-lib food provided through manual feeders. “It’s been a really steep learning curve, but we’re now weaning the piglets an average of 1kg heavier at 26 days, which should mean we can finish them at least a week earlier,” he says.
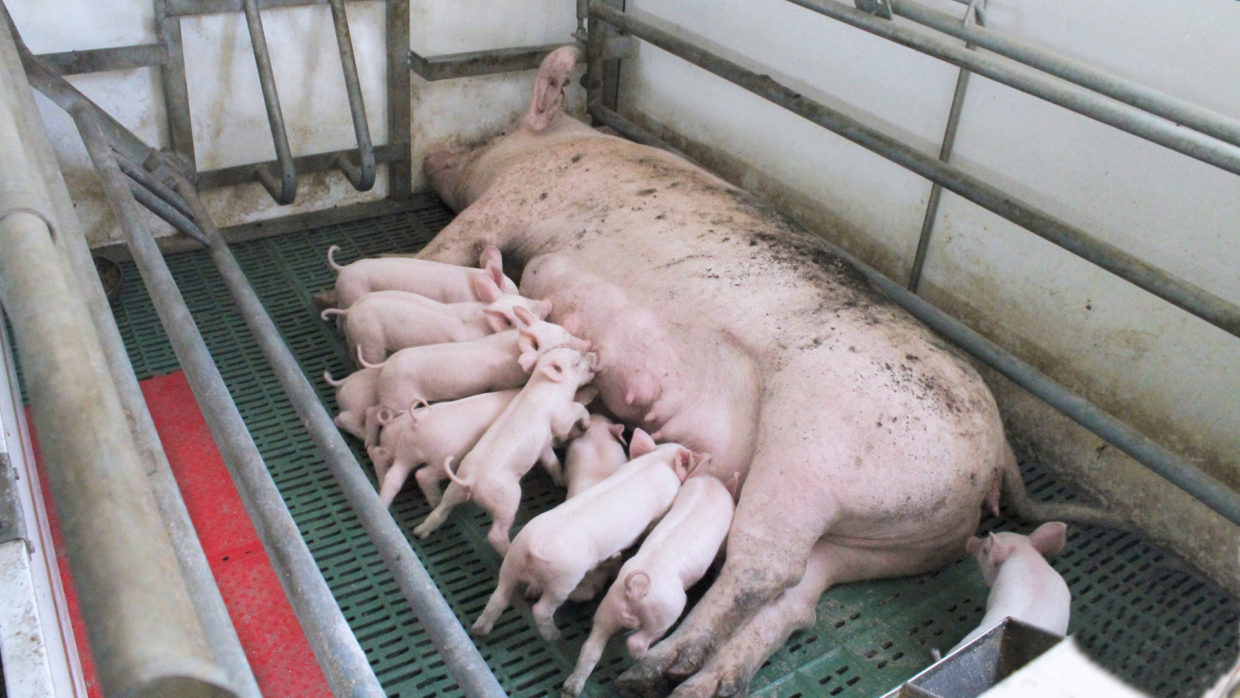
Weaning weights have improved significantly as the sows are happier and the piglets have better access to their teats, boosting milk yields.
Happy pigs do better
Mr Lasseter attributes the heavier weaning weights to the sows being more relaxed and the piglets having better access to their teats. “Happy animals do better. I think the piglets are suckling more, which is making the sows produce more milk. The sows are eating a huge amount more and really seem a lot happier.” He is also working with the AHDB levy board and research facility FAI Farms on trials using CCTV for the Co-op supermarket to study best practice and sow behaviour in the 360° pens.
Because the pens are more spacious, the staff can get in with the sows and piglets, rather than having to do everything behind bars. “That’s really initiated a relationship with the sows that we didn’t have before. They’re very quiet and don’t see us as a threat, which is really important.”
I think the whole industry will be moving to free farrowing in the future – the 360° pen is the most important development since the farrowing crate.
Robert Lasseter
Working indoors is also far nicer than dealing with the changeable British weather, he adds. “Although we’re short of labour right at the moment, we’re all a lot less stressed. Working with the sows now is a real pleasure.”
The sows remain in the pens for 26 days after farrowing, after which the piglets are weaned and moved into a converted cattle shed. As they grow they are moved again into straw-bedded pens housed in a large general purpose building, before being finished at about 80kg deadweight. Mr Lasseter keeps replacement gilts in groups, and uses Regumate to synchronise them before artificially inseminating them. “We’ll AI them twice and then turn them out with a boar.”
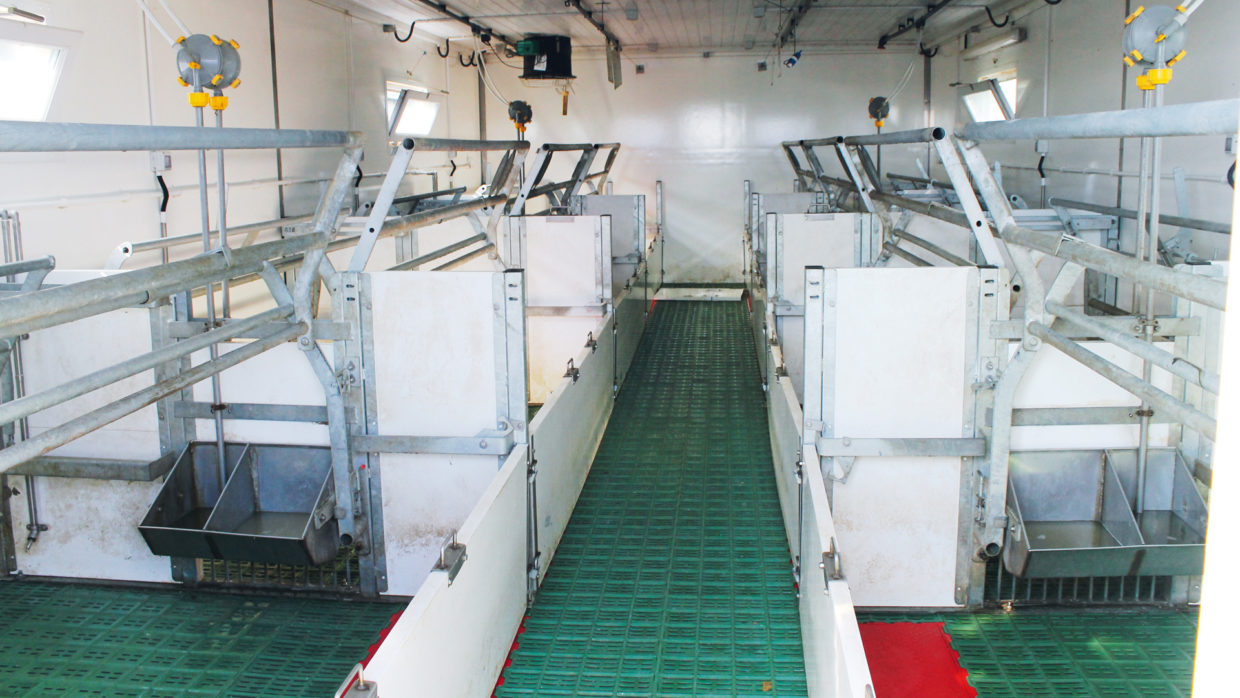
The sows farrow in three-week batches and the all-in, all-out system followed by disinfection has reduced expenditure on vaccinations.
Groups eliminate bullying
After their first litter, Mr Lasseter keeps the young sows together in outdoor pens to eliminate any bullying by older sows. “That makes a massive difference – we no longer get any second parity drop-off in production. They then join the main indoor sow herd after their second litter.” To keep costs down, Mr Lasseter produces all of his own cereals and straw, growing 130ha of winter wheat, winter barley and spring barley, with spring beans as a replacement to bought-in soya.
“I want to produce as much of my own feed as possible, but I do buy in some creep and grower feed as I don’t seem to be able to create a diet that’s good enough for pigs up to 20kg. If you can get them off to a good start it makes a huge difference.”
Mr Lasseter weighs all of his piglets at weaning and again six weeks post-weaning. “We used to just weigh an average group, but now we’re weighing every litter and we’ve realised that some sows are producing twice as much pig meat as others,” he says. “We always selected our gilts from sows using number of piglets born alive and weaned, as well as fertility – now we’re adding in litter weights as well.”
Corton Farm in figures
- 160ha farm with 130ha producing wheat, barley and beans
- 200-sow indoor pig unit
- Piglets born alive: 13.5
- Weaning 11 piglets (sows 10.5, gilts 11.3)
- Average weaning weight: 8kg
- Finishing 5000 pigs a year
Huge genetic potential
The new farrowing pens are also revealing the sows’ true genetic potential, with some weaning 15 piglets, and a top 26-day litter weight of 145kg. “We had no idea that some sows had the potential to do that. And the potential of our gilts looks even better, so there’s plenty more to come,” says Mr Lasseter. In a bid to further improve productivity, he is serving more sows over a slightly extended period, and has upped his replacement rate to bring gilts through more quickly. “We’re also selecting gilts with 16-18 nipples in preference to those with 14.”

“Happy animals do better”, says Mr Lasseter.
For this year Mr Lasseter is budgeting to sell 21t of pig meat (deadweight) every three weeks from 27 sows farrowed; in 2014 he averaged 15.8t. “It’s not a big f
The sows farrow in batches three weeks apart for ease of management, and the all-in, all-out system followed by cleanout and disinfection means Mr Lasseter has been able to reduce expenditure on vaccinations. “I like simple systems – plus all the jobs on the farm must be able to be carried out by a girl. You’re doubling your potential workforce, and women are really good with the young stock. I really like having a young workforce because they have bags of enthusiasm and loads of ideas.”
It is essential sows have only one type of farrowing pen so they can learn the system, he warns. “This makes it a more difficult financial challenge to change from crates, but unless all are changed the benefits for staff and sows won’t come through.”
arm, but when it comes to profit in pigs it’s all about the numbers. When prices are low you can lose a lot, but when they are good you can recoup a lot and reinvest, which is what we did in 2014,” he adds. “Our return on investment in the farrowing pens will be 10 years or more, but I think the whole industry will be moving to free farrowing in the future – the 360° pen is the most important development since the farrowing crate.”
Key benefits of free farrowing
- Allows sows to exhibit their natural behaviour
- Piglets suckle more, boosting weaning weights – by 1kg at Corton Farm
- Work in the pen, with the sow, not from outside a crate
- Happier pigs, happier workforce – less stress all round
- Higher welfare system preferred by consumers
- Potential for premium price through RSPCA assurance