Mr Steiner; until now, the idea of “Connected Support” has not really been promoted by John Deere. What are the reasons behind this?
That’s true, in the past we have used Connected Support Connected Support at most as a partial feature, for example Expert Alert. In order to provide Connected Support as a service, we essentially needed three elements that work together: Firstly, a telemetry-enabled machine, which allows the transmission of data collected on the machine being used, as well as the customer’s consent to transmit the data. Secondly, we needed special John Deere tools, able to automatically evaluate the machine data; and thirdly, trained John Deere sales partners. The sales partners can then carry out Connected Support based on the data evaluation – sometimes even without a mechanic needing to be on-site.
For Connected Support, we need three elements: A telemetry-enabled machine, special tools from John Deere and trained sales partners.
Which John Deere machines are telemetry-enabled and what does that mean exactly?
All tractors from the 6M, 6R, 7R, 8R, 9R series; the combines from Zweibrücken (Germany) and the USA; as well as the self-propelled forage harvesters and self-propelled sprayers, can be equipped with the JDLink telemetry module.
A total of about 215,000 machines are equipped with JDLink worldwide. JDLink should not be confused with the StarFire Receiver, which is required for precision farming. JDLink is used solely for the transmission of machine data collected from sensors attached to the machine, for example. You can think of it as a mobile phone that simply transmits data.

Connected Support
Start your work every day with the good feeling that experienced and trained experts take care of you and your machines.To Connected Support
Where is the data transferred to?
The machine data is first made available to the customer via their MyJohnDeere account. John Deere has developed special applications like the Operations Centre which allow the customer to read and process their machine data (e.g. fuel consumption, performance values or geographic locations). If the customer has also given their consent, the machine data provided via JDLink can be further analysed and evaluated.
For this purpose, John Deere has developed algorithms for error detection and machine optimisation based on historic and anonymised machine data. These algorithms automatically identify signs of possible technical or performance-related problems with the machine. If a potential machine problem is detected in this way, the system generates what is known as an Expert Alert, which is forwarded to the responsible sales partner.
What happens then with the Expert Alert?
The Expert Alert is transferred to the Machine Dashboard of the sales partner who is assigned to the customer or machine. On the Machine Dashboard, the sales partner can see the status of their customers’ JDLink machines. A list is displayed on a screen and constantly monitored. The list is ordered in such a way that the most serious faults appear at the top and are therefore easy to identify. Each individual Expert Alert describes both the symptoms that are appearing on the machine and the underlying problem. The Expert Alert simultaneously suggests a solution to rectify the fault. It also lists any spare parts required for a repair.
The data from a customer’s machine will only be automatically analysed by the algorithms to generate an Expert Alert and displayed on their distributor’s Machine Dashboard if the customer has given their consent.
Does every JDLink machine automatically appear on the list or does the customer have to do something?
John Deere takes the topic of data protection very seriously. The data from a customer’s machine will only be automatically analysed by the algorithms to generate an Expert Alert and displayed on their distributor’s Machine Dashboard if the customer has given their consent. Only with such consent can customers benefit from the potential of John Deere Connected Support and receive proactive support from their sales partner.
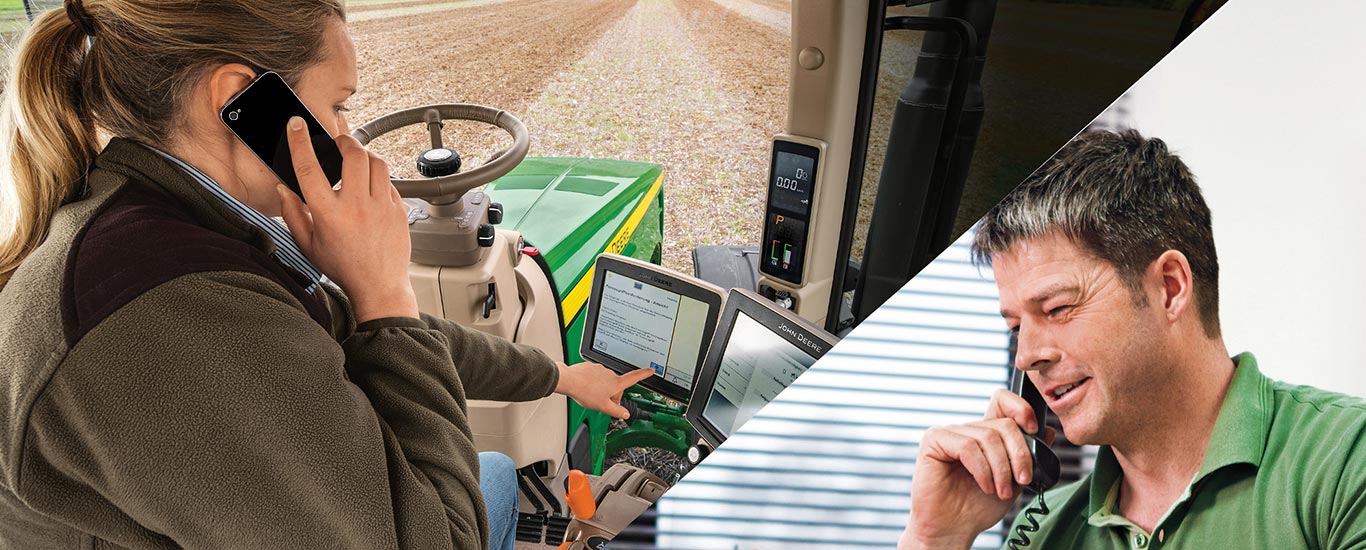
With Connected Support, the sales partner can access the customer’s machine display from the office. This means problems with the machine can often be solved straight away.
So, what does Connected Support look like?
That depends on the individual situation. If an Expert Alert appears, the machine is normally still functioning. The sales partner contacts the customer and discusses the next steps, for example by arranging a workshop repair or a repair on the machine directly at the customer’s premises. Sometimes it is necessary to carry out further diagnostics on the machine to properly prepare for a repair. Service ADVISOR Remote allows these diagnoses to be made without an engineer being on site. The repair can be prepared while the machine is still working. This minimises downtime.
Are there other forms of Connected Support?
Sometimes a customer simply needs a software update or is not satisfied with the performance of a machine that is still fully functional. In such cases, the sales partner can connect directly to the customer’s machine from the office using Remote Display Access (remote support) to optimise the machine settings. If necessary, the sales partner can also carry out a software update with the help of Service ADVISOR Remote.
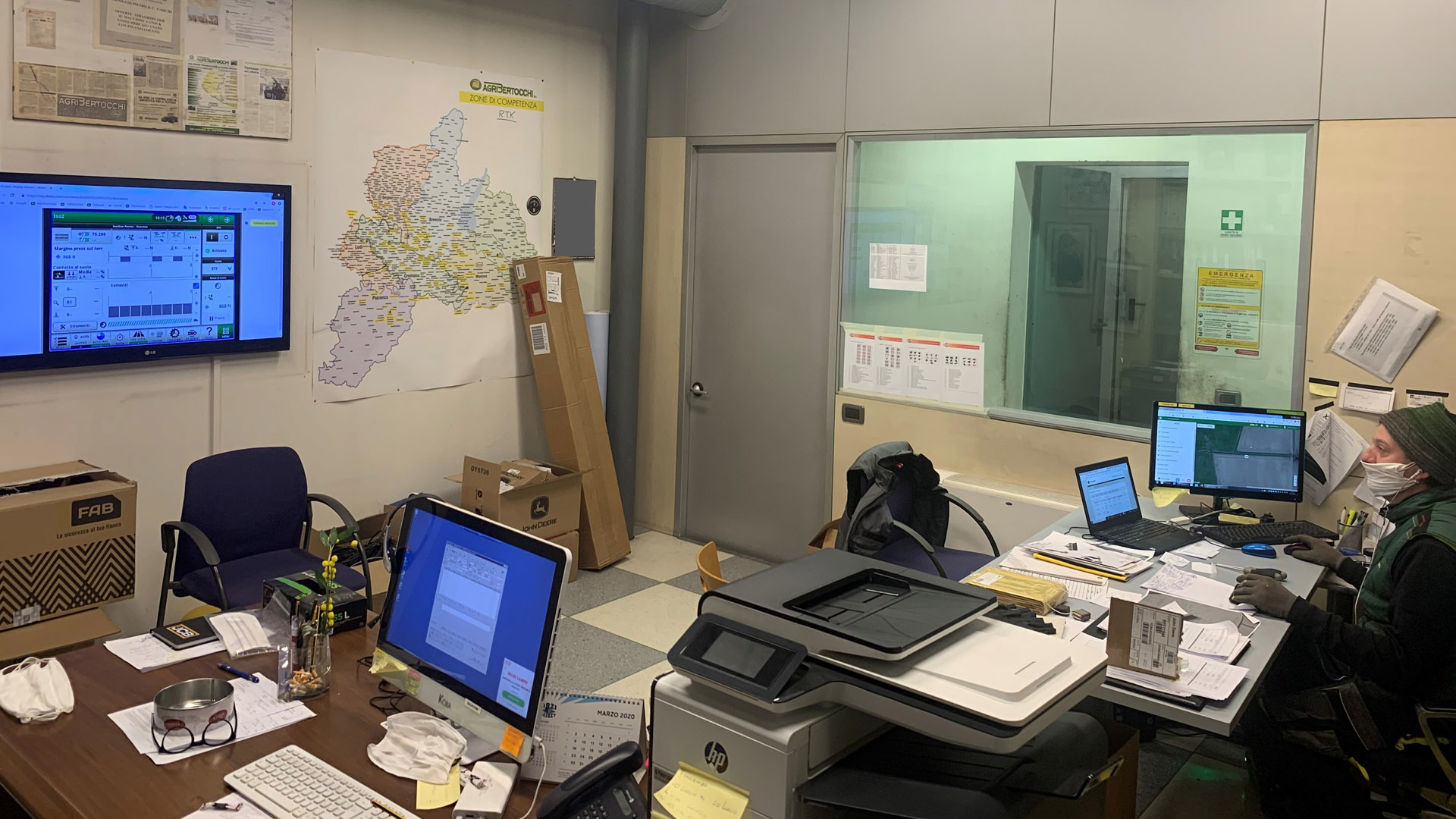
The North Italian distributor AgriBertocchi assists a customer in adjusting their new John Deere 1725NT maize planter directly from the office.
John Deere Connected Support also serves to keep machine downtimes as low as possible and to fully exploit the machine’s performance potential. But what does this have to do with coronavirus?
As we all know, northern Italy has been very heavily impacted by the coronavirus pandemic. Strict lockdown rules are in place and our sales partners are not allowed to visit their customers. Our Italian marketing manager told us about an instance near Bergamo where a new type 1725NT maize planter was delivered to a contractor. The initial set up of this machine is very complex and time-consuming and was completed solely using Remote Display Access. By the end, the machine was perfectly set up and the customer was fully able to work. Without the Connected Support of the John Deere sales partner, this would not have been possible in current times.